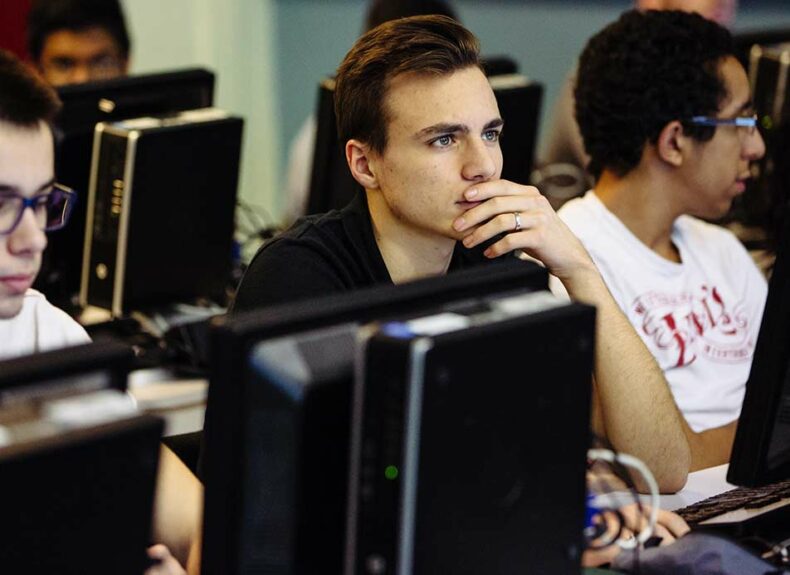
Un premier brevet déposé par l’IPSA dans le cadre du projet PERSEUS mené avec le Centre national d’études spatiales (CNES)
Responsable du Laboratoire de Mécatronique de l’IPSA et coordinateur du macro-projet ARES associé au projet PERSEUS du Centre national d’études spatiales (CNES), Sylvain Pernon vient de déposer un brevet, le premier du laboratoire.
Tout d’abord, peux-tu rappeler ton rôle au sein du projet PERSEUS mené avec le CNES ?
Il faut savoir que PERSEUS est décomposé en un certain nombre de macro-projets, chacun d’entre eux correspondant à une activité définie : il s’agit d’études diverses – comme par exemple des outils spécifiques de calculs -, de démonstrateurs sol – comme par exemple un moteur testé sur banc d’essai – ou alors de démonstrateurs vol. Dans cette troisième catégorie, on a des fusées, lancées depuis le sol ou aéroportées et des démonstrateurs de lancement aéroporté, autrement dit des porteurs autonomes sous la forme d’avions embarquant une fusée ; celle-ci est ainsi larguée depuis le porteur et lancée en altitude sur une pente définie. Dans mon cas, je suis coordinateur des démonstrateurs fusées de la famille ARES.
Ce brevet déposé concerne-t-il justement le macro-projet ARES ?
Oui, directement même : PERSEUS étant un projet incorporant les étudiants, les maîtres-mots sont modularité et innovation. Dans le cadre d’ARES, on fait du développement technologique : il s’agit donc d’essayer de trouver des solutions innovantes à nos problématiques et de démontrer qu’on peut faire les choses différemment, notamment en ce qui concerne la structure des fusées.
Les fusées ARES étant des petits gabarits (un diamètre de 160 mm et une longueur de 4/5 m pour les plus longues), nous arrivions à une limite technologique sur les matériaux composites utilisés pour le fuselage. En gros, pour qu’une fusée – qui utilise un matériau composite simple comme la fibre de carbone – résiste en vol, on pourrait s’amuser à descendre à des épaisseurs très, très fines… sauf que, du coup, la fusée deviendrait trop souple. Certes, elle serait suffisamment résistante mais serait aussi toute molle : ce serait comme essayer de faire voler un chewing-gum ! Elle ne suivrait alors pas du tout sa trajectoire nominale et cela aboutirait forcément à sa destruction finale. Ce brevet apporte une solution à ce problème et permet d’obtenir un gain de masse en plus d’un gain de vitesse.
En quoi consiste cette solution ?
Pour pallier ces problèmes, nous utilisions jusque-là des tubes en carbone qui étaient un peu surdimensionnés par rapport à l’application. L’idée, c’était donc de développer des tubes plus rigides pour une masse équivalente ou alors plus léger pour une rigidité un peu inférieure mais encore suffisante pour notre application. Nous sommes ainsi partis sur la fabrication de tube « en sandwich » selon une technique particulière de matériaux composites qui consiste à mettre une âme entre deux peaux en fibre de carbone, par exemple. Cette âme ne serait pas forcément très résistante mais servirait de support entre les deux peaux pour les éloigner l’une de l’autre. Dans l’industrie, il existe déjà des techniques de fabrication de tubes en sandwich mais sur des très gros diamètres. Pour ces petits diamètres, les techniques existantes sont souvent très artisanales ou alors comportent un certain nombre de défauts : l’application la plus typique est de mettre une âme en nid d’abeilles entre les deux peaux de carbone, or cela demande un savoir-faire et un type de matériel bien spécifiques. L’autre problématique, c’est que, si cette plaque est au départ en 2D, on vient l’enrouler ensuite autour du tube en 3D et, du coup, il y a forcément une couture qui se crée quelque part. Cette couture peut être soit une faiblesse, soit un sur-renfort par rapport au reste de la structure, ce qui fait que cette dernière n’est pas homogène. Nous avons donc trouvé une solution pour fabriquer ces tubes en sandwich sans les contraintes des techniques existantes et avec un coût relativement faible puisque cette méthode ne nécessite par l’utilisation de cuve ou de four de cuisson comme cela se fait avec les matériaux composites.
Comment avez-vous procédé ?
Plutôt que de partir sur une âme existante qu’on viendrait coller entre les deux couches de carbone, nous avons voulu fabriquer directement l’âme sur le composite. Dans notre procédé, nous fabriquons le sandwich couche par couche. Pour le matériau de notre âme, nous avons choisi une résine mousse époxy. En fait, quand on utilise cette résine sous forme brute, elle a une forme liquide, un peu pâteuse. Après son application, elle gonfle et cela crée une sorte de matériau un peu cellulaire, quelque chose de plus allégé que l’eau. La mousse vient englober la première couche de carbone et, ensuite, on vient fabriquer la deuxième couche par-dessus. Le brevet porte vraiment sur ce procédé de fabrication de sandwich au fur et à mesure.
Depuis quand utilisez-vous ce procédé ?
Depuis 2010, nous fabriquons toutes nos fusées ARES à partir de ces tubes, y compris la fusée supersonique SERA1 lancée avec succès en Suède au mois de mai 2014. Si nous n’avons pas déposé le brevet plus tôt, c’est tout simplement parce que nous avions mis en place ce procédé sans se demander s’il valait réellement quelque chose. Pourtant, au bout de deux-trois ans et à force de regarder ce qu’il se faisait autour, nous nous sommes rendus compte qu’il n’existait pas grand-chose de similaire. Après avoir vérifié que cette technique était brevetable, nous avons déposé le brevet.
Même si d’autres brevets ont déjà été déposés dans le cadre du projet PERSEUS, celui-là est le premier brevet déposé par le Laboratoire de Mécatronique de l’IPSA. C’est une fierté ?
Pour moi, oui. Il valorise beaucoup le travail réalisé et s’agit d’une reconnaissance de plus pour le laboratoire. Ce brevet a d’ailleurs été déposé en copropriété IPSA-CNES, ce qui signifie qu’il est passé en commission interne au CNES afin de décider de son dépôt. Le CNES a donc vu qu’il y avait un réel intérêt autour. C’est forcément très gratifiant.